TM 55-8115-200-23&P
CHAPTER 3
DIRECT SUPPORT MAINTENANCE INSTRUCTIONS
Section I. REPAIR PARTS, SPECIAL TOOLS AND EQUIPMENT
3-1. Special Tools and Equipment. No special
Appendix C of this manual.
tools or equipment are required.
3-3. Fabricated Tools and Equipment. No fab
3-2. Repair Parts. Repair parts are listed in
cated tools or equipment are required.
Section II. GENERAL MAINTENANCE
3-4. General. This section contains general mainte-
nance instructions to be used in performing direct
support maintenance on the container.
3-5. Maintenance.
a. Cleaning. All parts should be cleaned in accor-
dance with instructions contained in TM 9-214.
b. Inspection. The importance of carefully
inspecting disassembled parts cannot be over-empha-
sized since reassembly of substandard or defective
parts can result in needless troubleshooting and
rework. Structural surface dimensions and bore
diameters are to be inspected after cleaning. Areas to
be inspected for dimensions and tolerances shall be
free of surface treatment or painting at the time of
inspection. Inspection procedures must be performed
by experienced personnel using good shop practices.
Good shop practice includes the compilation of com-
plete and accurate inspection records as specified in
DA Pam 738-750. Such records not only expedite
reworking of the equipment but ensure a complete and
thorough overhaul. Inspection records should be based
upon the requirements outlined in this paragraph.
Parts requiring repair or replacement should be so
tagged and a notation of the disposition of these parts
should be entered in the inspection records. All
micrometers, gages, indicators, and other measuring
and testing equipment must be checked periodically
and, when required, accurately calibrated in accor-
dance with MIL-STD 120 or in accordance with the
recommendations of the equipment manufacturer.
NOTE
Parts marked serviceable at inspec-
tion should be treated with an
approved preservative if they are
not to be reassembled immediately.
NOTE
Surface rust and minor paint deteri-
oration, with rust showing through
is acceptable.
(1) Metallic parts. The below listed proc
dures are standard procedures that should be followed
when inspecting metallic parts.
(a) Ferrous parts. All ferrous parts
should be inspected for cracks by performing a mag-
netic particle test as specified in Specification MIL-I-
2513C.
(b) Non-ferrous parts. All non-ferrous
parts should be inspected for cracks by performing a
penetrant test as specified in Specification MIL-I-
2513C.
(c) Radiographic
inspection. Welds
shall be radiographically examined in accordance with
Specification MIL-R-11468, Standard I, for 100 per-
cent of the weld length.
(d) Magnetic
particle
inspec-
tion. Cracks or crack type defects are not permitted.
Magnetic particle inspection shall be performed in
accordance with Specification MIL-I-6868.
(e) Rust. Inspect all ferrous parts for rust
and rework as necessary.
(f) parts with external threads. Inspect
these parts for damaged threads. If threads are dam-
aged the part must be replaced.
(g) Threaded holes. Visually inspect all
threaded holes for threads and obstructions which
may be wedged at the bottom of the hole.
(h) Sheet metal parts. Inspect all sheet
metal parts for bent corners, distortion, cracks, tears,
broken corners, and defective welds.
(2) Hardware. Discard all cotter pins and
lockwashers during disassembly. Visually inspect all
nuts, bolts, and screws for damaged threads and heads
that could prevent proper wrenching. Replace all dam-
aged hardware.
Change 4 3-1
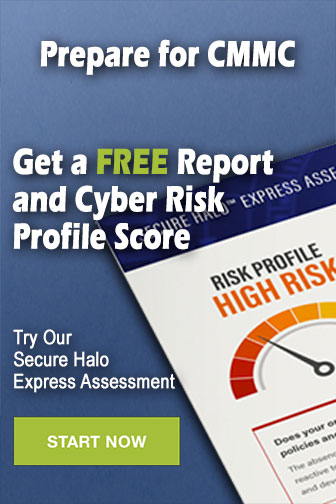